All dust is unique and must be tested to reduce the risks associated with combustible dust. Factors such as particle size, Kst, Pmax and MIT have a major impact.
Without a complete understanding of the unique factors to the facility’s dust, any system used to process your dust is in danger.
The characteristics of combustible dust are complex and unique at each and every point in your processing system.
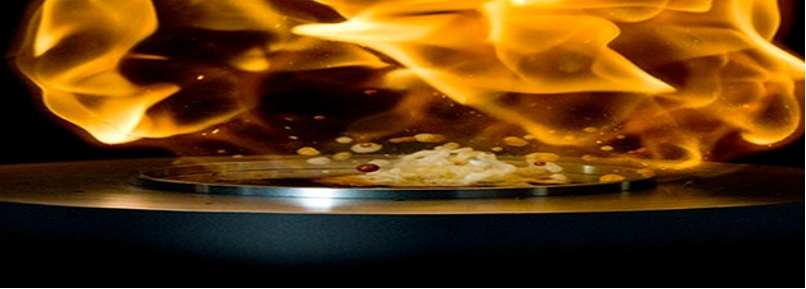
Ignition temperatures for common flammable dusts and fibers
MIT Layer
… or the Smoldering temperature
The smolder temperature describes the flammability behavior of a flat dust layer on a hot surface.
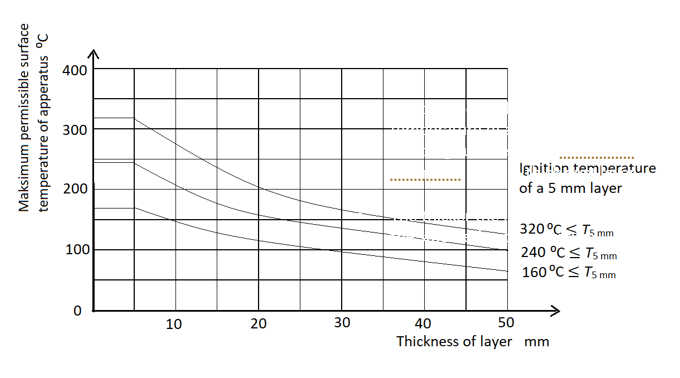
MIT Cluod
The minimum ignition temperature (MIT) is the lowest temperature of a hot surface that will cause a dust cloud, rather than a dust layer, to ignite and propagate flame. The test follows EN 50281.
Approximately 0.1 g of combustible dust is placed in a dust holder at the top of a temperature controlled furnace with an open bottom. The dust is dispersed by compressed air downwards past the hot surface of the furnace to see if ignition occurs and flames are produced. If the dust does not ignite, the furnace temperature is increased and the test repeated until ignition of the dust occurs.
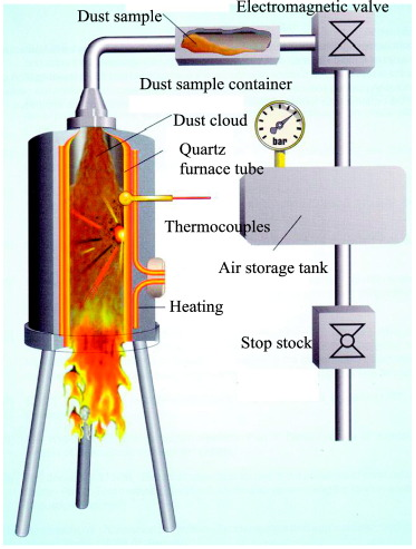
Once ignition has been established, the mass of the dust sample and injection pressure are varied to find the most vigorous explosive flame discharge. The temperature of the furnace is then reduced incrementally until flame propagation is no longer observed. At this temperature, the dust mass and injection pressure are varied to confirm that no ignition is found over ten consecutive tests. The minimum ignition temperature (MIT) is the lowest temperature of the furnace at which flame is observed.
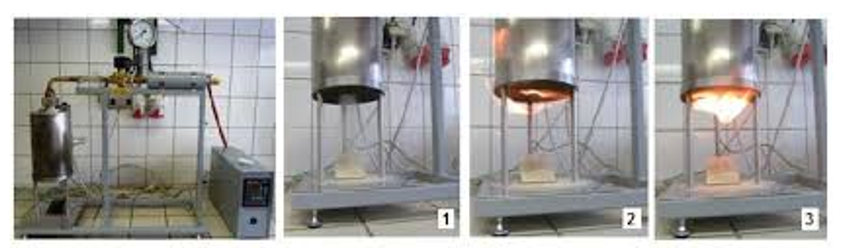
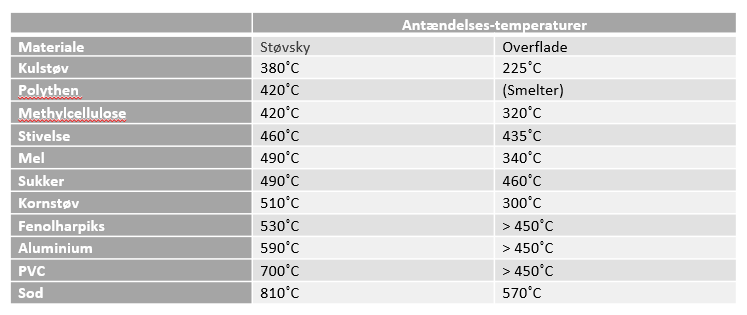
MIE – Minimum Ignition Energy
The MIE test measures the ease of ignition of a dust cloud by electrical and electrostatic discharges. The test is carried out according to EN ISO/IEC 80079.
Minimum power on dust can vary from less than 1 mJ (eg Aluminum dust) to several thousand mJ. Minimum power on energy depends on eg. type of fabric, grain size, temperature and moisture content.
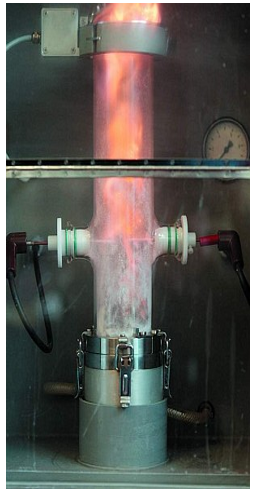
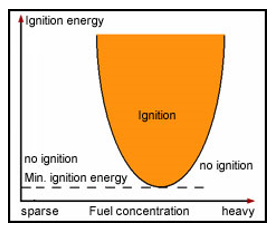
A weighed sample of combustible dust is blown up through the tube with compressed air past the ignition source. If flame propagation is observed, the energy of the spark is reduced until no flame propagation is seen.
The test result is stated as an energy range, indicating that ignition took place at the higher value and no ignition took place at the lower value.
The MIE is a measure of how sensitive an explosive dust cloud is to ignition. Testing for minimum ignition energy gives guidance on whether ignition by electrostatic discharge from plant personnel or process conditions is likely to occur in practice
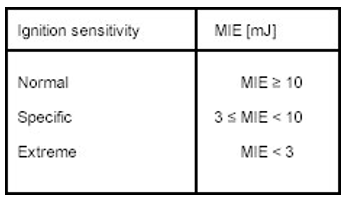
Kst is the deflagration Index for dusts, and the Kst test results provide an indication of the pressure rise at a dust explosion. The larger the value for Kst, the faster is the explosion.
Pmax is the maximum pressure reached during an explosion in a closed vessel
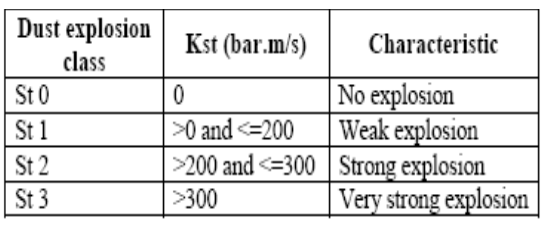
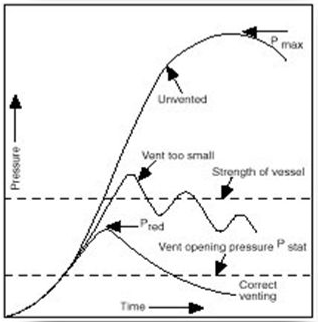
Approximately 300 grams of sample material are needed for the Kst test. In this test, dust is suspended in the 20-liter explosibility testing chamber and is ignited using a chemical igniter. The 20-liter testing chamber determines maximum pressure and rate of pressure rise if the sample explodes.
These parameters are used to determine the maximum normalized rate of pressure rise (Kst) and the maximum Pressure (Pmax).
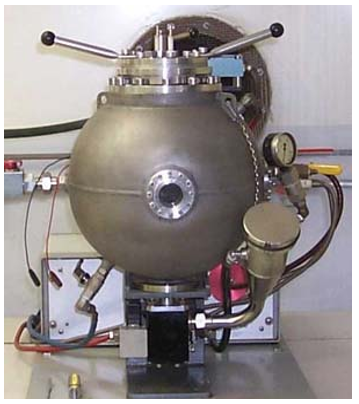
Dust type – Calculation and testing
All dust is unique and must be tested to reduce the risk associated with combustible dust. Factors such as particle size, Kst, Pmax and MIT have a big influence.
Without a complete understanding of the unique factors of different dust types, any system used to treat your dust is at risk.
The properties of combustible dust are complex and unique at every single point in your processing system.
We can offer Determination of dust explosion properties based on the latest standards. These parameters are used to determine the maximum normalized rate of pressure rise (Kst) and the maximum pressure (Pmax).
Calculation of the construction strength of containers (filter, silo, elevators, etc.)
An explosion relief is designed to prevent the explosion pressure in a container (or other closed volume) from exceeding the construction strength of the container, by possibly directing the explosion through an explosion relief in the walls of the container and to reduce the maximum explosion pressure (Pmax) to a reduced explosion pressure (Pmax). ), after an ignition. Generally, with a successful explosion relief, Pred will not exceed the design strength of the protected equipment. Explosion relief systems can be used on combustible gases, combustible mists, or combustible dust.
In order to be able to perform the correct size calculation on the unloading area, knowledge of the design strength of the protected container is required. It is often a challenge, and many will therefore only be able to come up with an estimate based on a guess and not any provable material. This often results in a forged calculation basis, with the possible catastrophic consequences. Based on dimensions, material and physical influences, we can prepare the necessary product documentation of the filter / container’s design strength, which is necessary for a correct calculation of explosion safety.